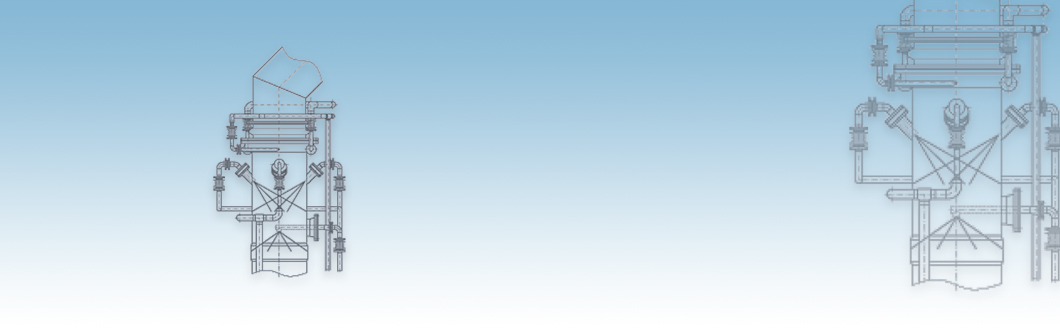
Gas Cleaning
Waste gas cleaning plants are a focal point of our scope of supply. Next to our core product of single and multi stage packing scrubbers we are delivering jet spray, nozzle spray and venturi scrubbers. For cooling and saturating hot gases different types of hot gas quenches are being applied.
All our components are manufactured by corrosion proof materials, mainly plastics. Due to the proved layout the use of plastic apparatus and components can be applied up to gas inlet temperatures of 1.300 °C.
We are well experienced in the separation of acid and alkaline pollutants like SO2, HCl, HF, HBr and NH3 as well as elemental halogens e. g. Cl2 and Br2.Our random packing scrubbing columns are being more and more used for the direct heat exchange between gases and liquids as a part of heat recovery systems.
Flue gas scrubbers are a very important element of our delivery program in the turnkey section. In addition to our core product, the single and multi-stage packed scrubber, we supply jet, spray and venturi scrubbers.
Various hot gas quenchers are used to cool and saturate the mostly hot gases. All equipment is made of corrosion-resistant materials, mostly plastic compounds. Thanks to tried-and-tested constructions, columns and internals can be built up to hot gas inlet temperatures of 1,300 ° C.
After the quench, the raw gas, saturated with water vapor, enters the actual absorption stage. The pollutant separation is preferably carried out in packed columns.
The raw gas flows through the column from bottom to top. Washing liquid is added in countercurrent to this. If necessary, chemicals are added to promote absorption.
Specially designed internals from our own production are at the heart of the column. In addition to modern distributor constructions, supporting and collecting elements, Hiflow® rings are used as random tower packing. Their open lattice structure makes them extremely resistant to dirt. Further advantages are their low weight, high load capacity and mechanical strength. The extremely low pressure loss also helps to save fan power.
In addition to flue gas cleaning, we also offer scrubber systems for separating inorganic and water-soluble organic pollutants from process gases and / or exhaust air flows.
Frequently occurring pollutants are, for example, HCI, HF, HBr, CI2, NH3, SO2. In addition, there are organic compounds such as alcohols (methanol, ethanol, isopropanol, etc.), aldehydes and ketones (e.g. formaldehyde, acetone), which are separated out in physical washes with water. We offer special absorption with organic detergents on request.
A suitable process management creates the most concentrated product solutions possible, some of which can be put to use.
The acidic and basic gas components are preferably separated in chemical washes, a chemical reaction taking place with the washing medium.
Depending on the application, the packed scrubber is preceded by a quenching stage in which the gas is cooled to saturation temperature by evaporation of water in direct heat exchange.
If there are high concentrations of pollutants in the raw gas, the circuit line can also be equipped with a heat exchanger in order to dissipate any heat that occurs from the system.
The leaching of highly concentrated hydrogen chloride offers a special feature. Here we can also offer systems for the recovery of hydrochloric acid, taking into account thermal aspects.
For the separation of SO2 / SO3 we offer a multi-stage reaction with H2O2. This produces sulfuric acid.
Another example of the recovery of valuable substances are scrubber systems for separating ammonia from exhaust air flows. The basic gas component is separated out in a chemical scrub with dilute sulfuric acid and reused as liquid fertilizer.
RVT supplies systems for exhaust gas and process gas cooling through direct heat exchange.
Hot gas is passed over a wetted surface in direct contact with cooled circulating liquid and is cooled to below the saturation temperature. The thermal energy changes into the liquid phase and is transferred to a customer's hot water system using external heat exchangers.
At the same time, the condensation results in the desired dehumidification of the gas. In numerous systems, this heat recovery takes place through direct heat exchange in the pack simultaneously with the mass transfer of an absorption process. In our systems, countercurrent columns are preferably used, in which a large heat and mass transfer surface is achieved using random packings or specially developed packings.
Another way of using waste heat is to generate steam, hot water or thermal oil. Suitable heat exchangers such as waste heat boilers are used for this purpose.